A shoe sole may wear out and crack or break due to the strain generated by the flexing action of the foot. Cracking or fracturing can also occur from sharp edges cutting notches and punctures, which will gradually turn into cracks during continuous flexion. It is therefore important to test the flex-crack resistance of shoe soles, and the Bennewart method is one of the methods used to test the resistance of shoe soles to cracking.
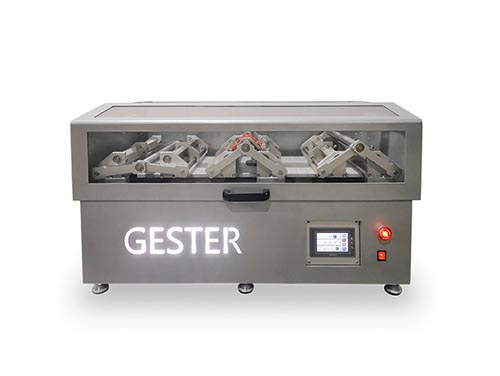
Sole flexing tester is used to measure the flexing resistance of shoe soles under continuous motion. Before the test, several holes are drilled at the position of maximum bending and Mount the specimen between two fixtures: a fixed clamp and a movable actuator. The specimen bends with the movement of the machine. After a certain number of test cycles, the specimen is removed and the difference in cut length is checked.
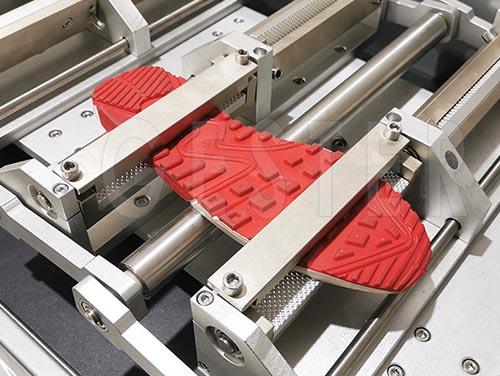
Test Steps
- Preparation of samples: Select the sole samples that meet the standard requirements and Cut specimens to dimensions specified in ISO 17707. A minimum of 3 specimens are required per test.
- Sample fixing: Fix the sole sample on the testing machine to ensure it is flat, vertical and stable. At the maximum bending stress line of the anti-slip pattern of the sole, use a notching knife to penetrate three small openings.
- Setting parameters: Adjust the test parameters such as bending angle, frequency and test times of the Shoe Sole Flexing Resistance Tester.
- Start test: Start the bennewart flexing machine and perform several bending tests. During the test, the degree of deformation and cracks on the sole should be carefully observed.
- Evaluation of results: After the test is completed, use a magnifying glass to inspect the degree of extension resistance of the sole, measure the final length of the cut on the surface of the specimen and compare it with the initial cut length. According to the standard requirements or product specifications, the test results are evaluated to judge whether the durability and bending performance of the sole meets the requirements.
- Record data: Record the test results, including test parameters, test results, sample information, etc., for quality control documentation.
Main technical Specification
- Bending angle: 90±2 , but can also be adjusted according to the test requirements.
- Mandrel diameter : 30mm, used to support the sole sample for bending.
- Bending speed: usually between 125-150cpm, but can be adjusted according to the test standard or demand.
- Width of fixture: to ensure stable fixation of the sole sample during the testing , the width is usually designed according to the size of the sole.
- Structure: The sole flexing tester usually comprises an electromechanical actuator, PLC control system, load cell, and specimen clamping assembly.
Precautions
During test, Strictly follow operational protocols to prevent equipment damage.
The test parameters should be selected and set according to the actual needs to ensure the accuracy and reliability of the test results.
After each use of the bennewart flexing machine, the sole flexing tester should be cleaned and maintained to ensure the normal operation and service life of the testing machine.