The high and low temperature, humidity, and heat test chamber employs a balanced temperature and humidity control method to achieve precise environmental conditions. It features stable and balanced heating and humidification capabilities, enabling high-precision temperature and humidity control at high temperatures. Equipped with an intelligent temperature regulator, the chamber uses a color LCD touch screen for temperature and humidity settings, allowing for various complex program settings. The program settings are set through a dialogue interface, making the operation simple and quick. The refrigeration circuit automatically selects the appropriate cooling mode based on the set temperature, enabling direct cooling and temperature reduction in high-temperature conditions. The base is constructed from welded channel steel into a grid frame, ensuring it can support the weight of the chamber and personnel under horizontal conditions without causing unevenness or cracking on the bottom surface. The chamber is divided into six surfaces and a double or single-opening door. The inner shell is made of stainless steel plate, while the outer shell is made of color-coated steel plate. The insulation medium is polyurethane rigid foam, which is lightweight, durable, and resistant to impact. The door is also made of color-coated steel plate, with handles designed for both internal and external opening, allowing test personnel to freely open the door from inside the enclosed chamber. This test chamber can record and trace the entire testing process, with each motor equipped with overcurrent protection and short-circuit protection for the heater, ensuring high reliability during operation. It is equipped with USB interfaces and Ethernet communication functions, meeting customers' diverse needs for communication and software expansion. The popular refrigeration control mode reduces energy consumption by 30% compared to the traditional heating balance control mode, saving energy and electricity. The chamber typically consists of a protective structure, air duct system, control system, and indoor testing framework. To better ensure the temperature reduction rate and temperature specifications of the high and low temperature humidity test chamber, a cascade refrigeration unit, which uses imported refrigeration compressors, is selected. This type of refrigeration unit offers advantages such as effective coordination, high reliability, and easy application and maintenance. When using this system, certain details should not be overlooked. What are these details?
1. Strictly abide by the system operation rules to avoid others violating the system operation rules.
2. Non-technical personnel are not allowed to disassemble and repair this machine. If disassembly and repair are required, the operation shall be carried out under the condition of ensuring power off and accompanied by personnel for supervision to avoid accidents.
3. When opening or closing the door or taking or putting the test object out of the test chamber, do not let the test object contact with the rubber edge of the door or the edge of the box to prevent the rubber edge from being worn.
4, the surrounding ground should be kept clean at any time, so as not to suck a lot of dust into the unit to deteriorate working conditions and reduce performance.
5. Attention should be paid to protection during use, and it should not be collided with sharp or blunt objects. The test products placed in the laboratory should be kept at a certain distance from the suction and exhaust air outlets of the air conditioning channel to avoid hindering the air circulation.
6. Prolonged inactivity can reduce the system's effective lifespan, so it should be powered on and operated at least once every 10 days. Avoid frequent short-term use of the system. After each operation, the system should not be restarted more than 5 times per hour, with each start-stop interval being at least 3 minutes. Do not open the door when it is cold to prevent damage to the door seal.
7. After each test, set the temperature near the ambient temperature, work for about 30 minutes, then cut off the power supply, and wipe clean the inner wall of the working room.
8. Regular cleaning of the evaporator (dehumidifier): Due to the different cleanliness levels of the samples, a lot of dust and other small particles will be condensed on the evaporator (dehumidifier) under the action of forced air circulation, so it should be cleaned regularly.
9. The condenser should be maintained regularly and kept clean. Dust sticking to the condenser will make the compressor dissipate heat poorly, resulting in high pressure switch jumping and generating false alarm. The condenser should be maintained regularly.
10. Regularly clean the humidifier to prevent scale buildup, which can reduce its efficiency and lifespan and cause blockages in the water supply lines. To clean it, remove the evaporator panel from the working chamber, use a soft brush to scrub the humidifier, rinse with clean water, and drain promptly. 11. Regularly check the test cloth of the wet bulb. If the surface becomes dirty or hard, replace it to ensure the accuracy of the humidity sensor's readings. The test cloth should be replaced every three months. When replacing it, first clean the water collection head, wipe the temperature sensor clean with a clean cloth, and then replace the test cloth. Ensure your hands are clean when replacing the new test cloth.
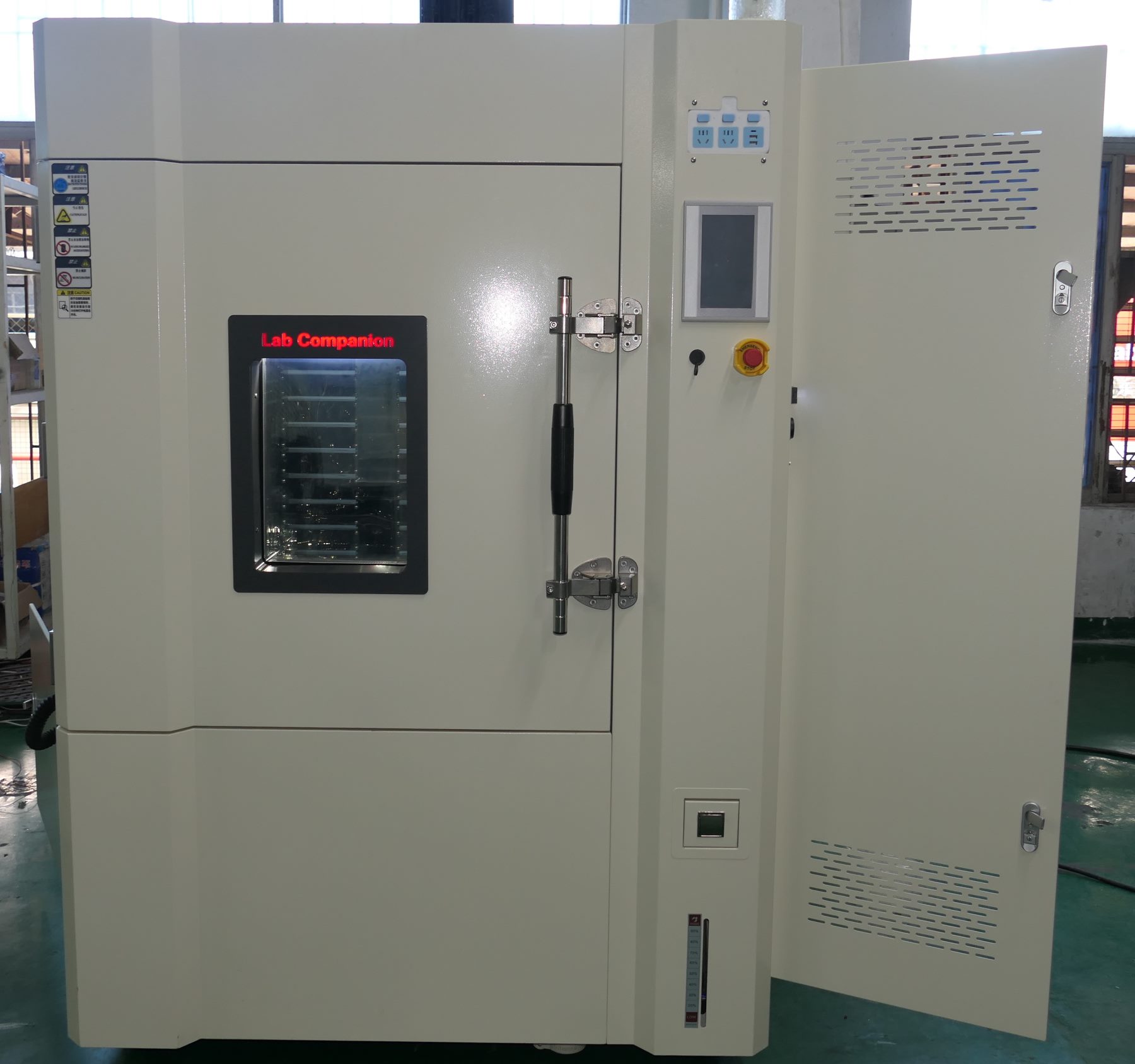